Our extensive manufacturing capabilities enable us to produce precision metallic powertrain systems, advanced aerial work platforms and durable industrial & agricultural assemblies.
Linamar global operations are divided into regional groups with vertically integrated operations combining expertise in light metal casting, forging, machining and assembly, metal forming for both the global electrified and traditionally powered vehicle markets.
Linamar has a diverse range of capabilities that are continually evolving to better meet the needs of a global market.
Machining & Assembly
- Advanced Automation & Robotics
- CNC Expertise
- Complex Assemblies
- Hydroforming
- Heat Treatment
Metal Forming
- Robotic Welding
- Laser cutting
- Metal Forming
- Stamping
- Painting
- Assembly
Forging
- Hatebur High Speed Hot Horizontal Forging
- Conventional Vertical Forging
- Cold Forming
- Ring Rolling
- Radial Forging
Light Metal Casting
- Gravity & Low Pressure Aluminum Die Casting
- High Pressure Aluminum & Magnesium Die Casting
Markets
Diversification is one of our strategies for success.
We envision a future where we continue to be competitive and diversify into six strategic markets. It is a 100-year plan geared to a changing world with a vision for continued, long-term sustainable growth. This is a vision meant to drive a positive impact for all the Linamar stakeholders.
McLaren Engineering is Linamar’s leading-edge technology and product development team for our mobility segment.
The foundation for Linamar’s technical advancements is rooted in the expertise of McLaren Engineering. Purchased by Linamar in 2003, McLaren provides design, development, integration, manufacturing, and testing capabilities that provide our customers a world-class, full-service supplier partner that develops complete vehicle powertrain & driveline systems for both the global electrified and traditionally powered vehicles.
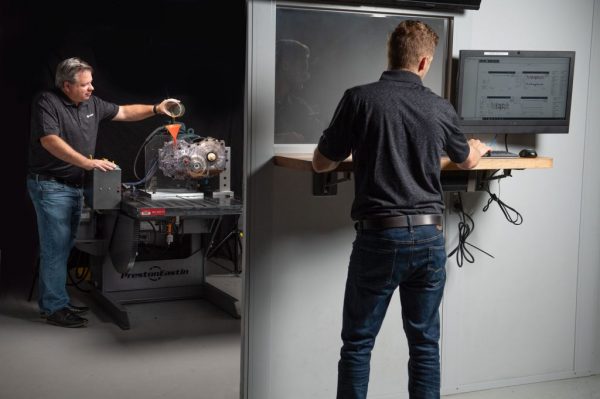
The Linamar Product Development System is a disciplined approach to the product development cycle as outlined by the Linamar GOS (Global Operating System) Playbook.
The step-by-step process begins with design creation through the use of advanced industry CAD and CAE software packages, followed by Design Validation (DV) and Production Validation (PV) level testing of physical parts in our own development facilities and lastly, the release of the approved production design into the Linamar manufacturing environment.
Linamar and McLaren collaborate during this process to ensure seamless integration from initial concept through to program end-of-life.
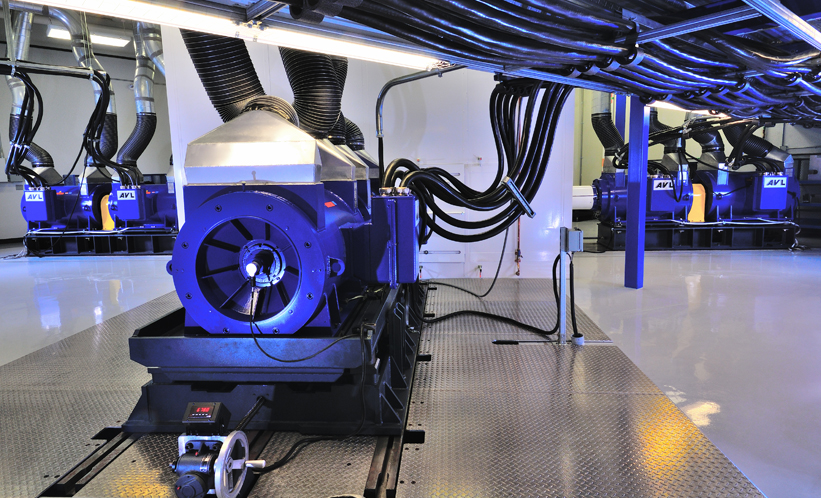
Rapid Prototyping
Specialty Fabrication and Low Volume Builds
Driveline TE Cell
Driveline NVH Cell
Rotary Actuator Cell
Engine Testing Services Matrix
Transient Engine Development Cell
Ancillary Capabilities
Thermal Studies
Impact Testing
eLIN
eLIN focuses on developing electrified product solutions for all business lines, developing electrification strategies in four key areas: Power Generation, Power Storage, Propulsion Systems, and Structural & Chassis offerings for electrified vehicles.
eLIN unified product solutions are driving advancements in electrification, leveraging Linamar’s capabilities, providing innovative solutions to our customers.
Linamar Global Locations
PRESS RELEASES
- 2025
- 2024
- 2023
- 2022
- 2021
- 2020
- 2019
- 2018
- 2017
- 2016
- 2015
- 2014
- 2013
- 2012
- 2011
- 2010
- 2009
- 2008
- 2007
- 2006
- 2005
- 2004
- 2003
- 2002
- 2001
- 2000
- Show all years
Diversified, Disciplined, and Delivering Linamar Generates Strong, Sustained Free Cash Flow
August 13, 2025Linamar Delivers Earnings Growth and Continued Free Cash Flow in Challenging Market
May 7, 2025Linamar Delivers Record Sales over $10 Billion, Exceptional Free Cash Flow and Another Year of Double-Digit Earnings Growth
March 5, 2025Linamar Announces Investments in Automotive Technologies Supported by the Canadian Federal and Ontario Provincial Governments
January 28, 2025Careers
Together, we are Powering Futures.